第一节 三牙轮钻头在井底的运动
在石油钻井中,牙轮钻头能适应各种地层的钻井,是主要的破岩工具之一。牙轮钻头在井底工作时的运动状态和受力状态是相当复杂的。国内外对牙轮钻头的工作原理,无论在理论研究或实验研究方面都作了大量的工作,这些研究成果为钻头的设计使用提供了依据。 三牙轮钻头在井底的运动,决定牙轮与牙齿的运动,也就直接决定牙齿对地层岩石的破碎作用。因此,在了解钻头破碎岩石的工作原理之前,首先应了解钻头在井底的运动。
一、钻头的公转 钻头牙轮绕钻头轴线作顺时针方向旋转的运动简称为钻头的公转。钻头公转的速度就是转盘或井下动力钻具的旋转速度。钻头公转时,牙轮绕钻头轴线旋转,牙轮上各排牙齿绕钻头轴线旋转的线速度不同,外排齿的线速度最大。
二、钻头的自转 钻头旋转时,沿着从牙轮底平面到牙轮尖部的方向看,牙轮绕自身的轴线作反时针方向的旋转称自转。牙轮的转动是岩石对牙齿的吃入破碎作用产生反作用的结果。牙轮自转转速的影响因素有公转转速、钻头结构、齿面结构、钻井参数和岩石性质等。一般情况下,牙轮自转的转速比钻头公转的转速快。把牙轮自转转速与钻头公转转速之比称为轮头比,轮头比的值一般在1--1.5之间。
三、钻头的纵振(轴向振动) 钻头工作时,对一个牙轮而言,牙齿与井底的接触是单齿、双齿交替进行的。单齿着地时,牙轮的轮心处于最高位置,双齿着地时则轮心下降。牙轮在转动过程中,轮心位置不断上下变换,使钻头沿轴向作上下往复运动,这就是钻头的轴向振动。纵振振幅就是轮心的垂直位移,它与牙齿的齿高、齿距等钻头结构参数及岩性有关。在软地层,牙齿吃入深、振幅小,硬地层则振动加剧。振动的频率与牙轮齿数及牙轮转速成正比。在旋转钻井中,钻头纵振频率一般为100~500次/min。 此外,由于井底不平,钻头产生振幅较大的低频振动。据国外资料介绍,低频振动的振幅就是井底凹凸部分的高差,一般为10mm左右,频率低于50次/min。低频纵振对钻头是不利的因素,在硬地层中会造成跳钻。牙轮钻头的纵振是上述两种振动之和,它构成了牙齿的冲击压入作用,破碎岩石,提高破碎效率。
四、横向振动 所谓横向振动,就是沿着垂直于钻头轴线方向的振动。造成钻头横向振动的因素很多,包括钻头与岩石互作用、钻柱的弯曲变形,钻柱的偏心旋转,钻柱质量分布不均匀、地层倾角以及井底岩石性质差异等等。钻头的横向振动对钻柱的横向振动有直接的影响,也是造成钻头失效的重要原因。
五、扭转振动 钻头的周期性运动导致扭矩成周期性变化,引起钻头周期性的扭转振动。钻头的扭转振动主要由钻头的粘滑运动造成的,即钻头旋转速度变化很大,在某一瞬时钻头可能静止不动,过一段时间后便以数倍于平均转速的速度旋转,这样就会引起钻头的失效,也可能引起钻柱的早期疲劳破坏。因此应尽量避免钻头出现这种现象。
六、牙轮的滑动 破碎不同类型岩石,对钻头要求不同的滑动量,可通过设计钻头时采用不同的结构及参数获得。对于一个牙轮而言,不同位置的齿排的滑动方向是不同的。外排齿及靠近外排齿的齿排,一般是正向滑动(假设钻头旋转,而牙轮不自转时,牙齿在井底的滑动就是正向滑动);牙轮尖部的齿排及靠近牙轮尖部的齿排一般是负向滑动;而在外排齿与尖部齿排之间的某个中间齿排或虚拟齿排做纯滚动。一般情况下,软地层钻头应具有较大的滑动量,硬地层钻头应尽量减少或不产生滑动,避免牙齿早期损坏。但是,由于钻头工作时,牙轮与牙掌轴颈的相对运动总是存在摩擦阻力等原因,即使设计的是纯滚动钻头,实际钻进中仍然存在着滑动。对纯滚动钻头作室内模拟试验,发现约有20%的滑动量。 上述几种运动是牙轮钻头在井下工作时同时发生的复合运动。实际钻进时,还有整个钻头的向下运动,其向下运动的速度就是钻头钻进的机械钻速。
第二节 钻头工作时的受力分析
前面已经分析了,钻头钻进时会产生纵向振动、横向振动及扭转振动。在每次纵向振动中,钻头上行压缩下部钻柱;钻头下行则钻柱恢复原长。其位能转化为钻头的动载荷。钻头工作时,牙齿作用到岩石上的力有静载荷(加在钻头上的钻压)及动载荷(钻头与下部钻柱速度下降而产生的动载)。也就是说牙齿冲击破碎岩石时,钻头受到岩石的反作用也等于静载荷与动载荷之和。而横向振动则可能引起钻头与井壁的碰撞,使钻头受到井壁很大的撞击力。
钻头在井下工作时,除了受到纵向静载荷和动载荷及横向载荷外,由于钻柱旋转,于是还受扭矩作用。当钻压较大,牙齿吃入岩石较深,尤其是牙齿在井底滑动较大时,钻头承受的扭矩更大。而扭转振动会引起钻头的扭矩的进一步增加。此外,还有牙轮背锥面及牙掌背部与井壁摩擦而产生摩擦力矩以及受钻头喷嘴喷出高压喷射液流的反力作用等。受力情况十分复杂,目前仍未能进行精确的计算。 近几年美国和俄罗斯等国家都在实验室内开展了钻头受力的试验研究工作。国内西南石油学院钻头研究所等部门也都进行了大量的试验研究工作,对牙齿及轴承的受力状况进行了测定,并取得了有价值的试验成果。通过实验,发现钻头三个牙轮承受的载荷不相等,而且差别很大,受力大的牙轮先期失效。因此,设计钻头时,应尽量使三个牙轮的切削结构合理布局,使三个牙轮的载荷分配趋于平衡。严格控制三个牙轮的高低差及轮背与钻头连接螺纹的同轴度误差。这样可使钻头工作平稳,延长牙轮及轴承的使用寿命。试验还测定出,钻头小轴颈载荷约为大轴颈的20~30%。因此,目前钻头设计已由原来的一道止推(小轴端面)承载改为二道止推(大轴台肩面)承载,这样就减少了大轴颈的径向载荷而延长了轴承寿命。 井下实测钻头承载情况表明:钻头在井下工作时受力情况变化很大。正常钻进时,钻压的变化通常是在平均钻压的25~50%范围内,有时最大钻压达到平均钻压的3.5倍。正常钻进时,钻头纵向振幅一般不大于1.6mm。但钻头工作不平稳时,振幅可增大至25mm。振动大时,钻头会短时离开井底,出现跳钻现象。因此,在下部钻具中安装减震器,减少不正常的钻压和扭矩的峰值,将有利于增加钻头的寿命。
第三节 钻头对岩石的破碎作用
一、三牙轮钻头的一般破岩方式 钻头在井底运动,除了公转和自转外,还有轴向纵振、横向振动、扭转振动及牙轮的滑动。这几种运动是钻井时同时发生、综合在一起的复合运动。三牙轮钻头就是在上述复合运动所产生的冲击、压碎作用及滑动剪切作用下破碎岩石的。 冲击、压碎作用 三牙轮钻头在井底工作时,由钻头纵振产生牙齿对岩石的冲击、压碎作用,是牙轮钻头破碎岩石的主要方式。钻头旋转时,牙齿以一定速度冲击压入岩石,牙齿压入岩石需要足够的比压与接触时间。牙齿与岩石的接触时间T,应大于岩石破碎所需时间T0,才能有效地破碎岩石。根据实测结果,目前现场所用设备的转盘转速范围内,T0一般都小于T,如脆性岩石,T0=(0.3~0.4)×10-3s;塑性岩石,T0≥2.5×10-3 s。当牙轮转速n=290r/min时,8 1/2 H517钻头外排齿与岩石的接触时间约为11.4×10-3 s。 钻进时钻头在井底产生纵振,使钻柱不断压缩与伸张,下部钻柱把这种周期的弹性变形能传递给牙齿,这就是钻头破碎岩石时牙齿冲击压力的来源。增加钻头牙齿对地层的冲击力有利于破碎岩石,但也会使钻头的牙齿和轴承受到损坏,使钻柱处于不利的工作条件。
2、滑动剪切作用 牙轮钻头工作时,由于钻头的结构及地层摩擦阻力,当钻头作公转运动的同时,引起牙轮自转。由于牙轮的自转是一种被动的转动,因而,钻头上与井底接触的某一点的公转线速度大于牙轮上同一点的自转线速度,因而产生滑动。这种滑动和汽车的被动轮打滑的原理是一样的。 牙轮在井底的滑动使的井底岩石产生剪切破碎。由于岩石的抗剪切的强度小于抗压强度,因而由牙轮滑动的破岩效率较高。为了提高软至中硬地层的破碎效率,除了要求牙齿对岩石有冲击压碎作用外,还要求有一定的剪切作用。超顶、复锥和移轴,使得钻头上与井底接触的某一点的公转线速度与牙轮上同一点的自转线速度的差值增大,有利于增加剪切破碎作用。所以要增加剪切破碎,应该使牙轮钻头具有超顶、复锥和移轴的结构,使牙轮锥顶不与钻头轴线重合。 牙轮锥顶超过中心的距离C叫超顶值如图1-1(a)。牙轮的超顶值越大,钻头的滑动剪切作用也就越大。牙轮超顶引起剪切作用的原因可用速度分析定性说明。
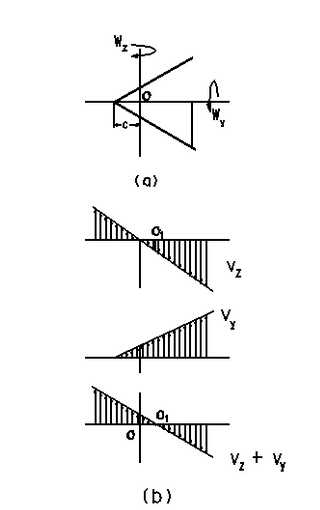
图1-1(b)为钻头公转与自转时二者的合成速度分布。
O1为纯滚动点,在01两侧的滑动方向是相反的。因此,超顶牙轮产生切线方向滑动。把由牙轮上与井底接触点到井底中心的连线方向称为径向,切向是指与上述径向垂直的方向。超顶值使牙轮产生切向滑动,切向滑动速度大小与超顶值C成正比。 复锥牙轮的副锥顶(延伸线)是超顶的,主副锥顶点的距离叫锥顶距。锥顶距越大,主副锥角之差值就越大,牙轮产生的滑动量也就越大。复锥产生滑动是由于复锥牙轮绕轮轴转动时的线速度呈折线分布,其与钻头公转时的合成线速度不为零。同样,在副锥上也有一个纯滚动点。牙轮锥体具有二个图1-1 超顶牙轮速度分析 或二个以上复锥时,使得牙轮则会产生切向滑动。 牙轮轴线与钻头轴心线在空间形成两条不相交的直线,这两条直线间的最小距离为偏移值。由于钻头具有偏移值s,于是牙轮在滚动过程中同时产生滑动,钻头偏移值越大,滑动剪切作用就越大。 牙轮移轴所产生的滑动可以分解为切向滑动和径向滑动。径向滑动可以剪切破碎井底各齿圈之间的岩石,切向滑动则与超顶和复锥牙轮产生的切向滑动一起,可以剪切破碎井底同一齿圈上的破碎坑之间的岩石。 牙齿的滑动可以剪切井底岩石,提高破碎效率,但同时也加剧了牙齿的磨损。轴向滑动使牙齿内端面磨损。因此,应根据齿的不同受力情况进行牙齿的表面强化,以提高其耐磨性。
二、牙齿对岩石的破碎效率及影响因素 钻井时岩石的破碎过程是异常复杂的,因为破碎工具的形状是多种多样的,而施加的又是动载,其大小及方向均随时间而改变。在井底的岩石还受岩石围压、钻井液压等多种力的作用。通过实验室的模拟实验,对钻井过程中岩石破碎的特点进行分析表明:“压入的破碎”在破碎过程中起主要作用。牙轮钻头的牙齿在轴向载荷作用下压入岩石(冲击动载过程),使齿面下的岩石产生体积破碎,形成坑穴;由于牙齿沿井底的滚碾作用,使破碎的坑穴不断扩大,加上水力作用不断剥离和清除岩屑,冲蚀并扩大岩石的破碎体积。对于切削或磨削型的钻头(刮刀钻头或金刚石钻头),既有在钻压作用下对岩石的压入,又有在钻头扭矩的作用下对岩石的切削。 所有同时与井底岩石相接触的齿顶面积总和构成了牙轮钻头的承压面积。钻井时岩石破碎的效率决定于牙齿上的比载荷和钻头的转速。如果比载荷太小或转速过高,都有可能形成不了体积破碎。
1、钻压对岩石破碎速度的影响 岩石的破碎过程大致划分为三个区段,牙齿单位面积上承受的钻压称为比载荷。钻进开始时,比载荷远小于岩石的硬度,比载荷P与机械钻速Vm成正比。此时,破碎的过程只具表面的性质,称为“表面破碎区”。 随着比载荷的增大,逐渐接近岩石的硬度值,牙齿每次对岩石的冲击,使井底岩石出现微裂纹,促进了破碎。当某处的岩石经过牙齿多次冲击而产生了体积破碎,此时机械钻速Vm增加较快。 当钻压已达到或超过岩石硬度值时,牙齿每次冲击作用都能使岩石产生体积破碎,称为“体积破碎区”。进一步提高钻压,可以使岩石发生二次体积破碎。这时机械钻速迅速增加,岩石破碎效率最高。因此,在钻进时选用的钻压,应避免造成低效率的表面破碎,而应达到最高效率的体积破碎。 一般地说,提高钻压有利于提高机械钻速,但这有个前提,就是要在承载能力范围内。 所以,最优的钻压就是,达到牙齿每次冲击作用都能使岩石产生二次体积破碎,又在钻头的承载能力范围内。
2、钻头转速对岩石破碎速度的影响 实验表明:对于低塑性岩石(如大理岩)和脆性岩石(如花岗岩),在所研究的转速范围内,其机械钻速Vm与钻头速度n成直线关系。对于高塑性及多
孔隙岩石(如白垩和多孔石灰岩),在相当低的转速时,其相互关系已偏离直线。其原因在于对塑性高及多孔岩石,其从变形到破碎,需要较长的时间,而牙齿与岩石的接触时间大约是几个毫秒。钻头的转速越高,则牙齿与岩石的接触时间越短。接触时间不足以使岩石达到完全的破碎,这意味着增大钻头转速时,钻头每转一圈所破碎的岩石深度就要减少。岩石的塑性系数越大,需要接触时间越长,因此,不宜采用很高的转速。当钻头类型选定之后,对于具体的特定岩层,存在一个最合理的钻压和转速的配合,以达到最高的破岩效率,而岩石不同的硬度和塑性系数是选择这两个参数的重要依据。
三、各类型钻头的主要破岩方式
(1)适用于极软至中软地层的钻头(如437、517、116、126型等)兼有移轴、超顶及复锥三种结构要素,主要靠牙齿的压入剪切作用破碎地层。
(2)适用于中软至中硬地层的钻头(如537、617、136、216型等),也是兼有移轴、超顶及复锥三种结构要素,但其偏移量及超顶值较小,靠牙齿的冲击、压碎作用及剪切作用同时破碎地层。
(3)适用于硬至极硬地层的钻头(如737、837型),其移轴及超顶值极小,甚至为零,多为单锥形牙轮,主要靠牙齿的冲击、压碎作用破碎地层。